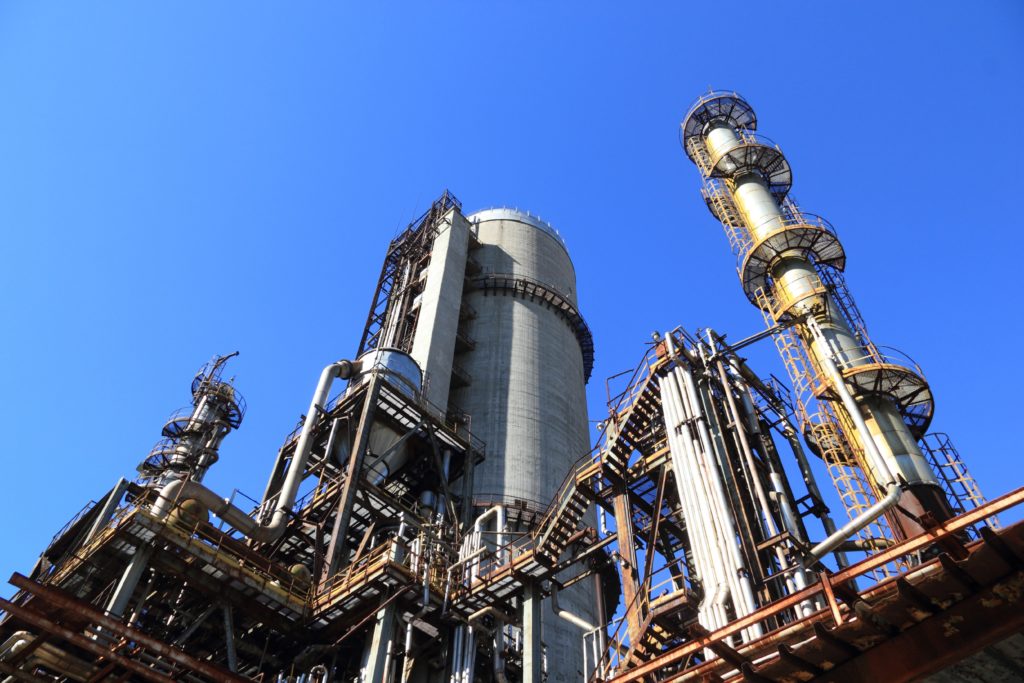
Click on any of the technical topics below to read or download
Cetane is a term referencing the ignition quality of diesel fuel. In the United States, the minimum Cetane is 40 while European Cetane is typically 52. Engine manufacturers prefer a Cetane of 45 or higher because it minimizes ignition delay, decreases hard starting, lessens white smoke at start-up, reduces engine knock, lowers fuel consumption, and enhances engine life.
In order to raise motor Cetane from 40 to 45 or higher, Cetane improver is added to the fuel. Cetane Improver is defined as 2-EHN, 2-Ethyl Hexyl Nitrate. Cetane Improver is a high energy compound. The auto-ignition temperature of No. 2 diesel is 518°F. and the auto-ignition temperature of Cetane Improver is 419°F. When Cetane is added to No. 2 diesel, the fuel will exhibit:
- Decreased engine delay
- Fast cold starts
- More complete combustion
- Increased power
- Reduced black smoke under load
Many Midwest refiners today are processing Western Canadian Select (WCS), commonly known as Tar Sands Crude. Typically, WCS is priced at $15-$20/barrel discount to West Texas Intermediate (WTI). WCS is a heavy, low paraffinic, high aromatic crude that has a typical Cetane of 33. As a result, refiners elect to add Cetane Improver at the refinery in order to raise the motor Cetane to a typical 42-43.
This addition of Cetane Improver by refiners significantly reduces the Cetane improvement when additive packages are added by Jobbers, Fleets, or at Retail since the first Cetane bump is usually all a fuel can be boosted. Premium diesel additive packages containing Cetane continue to be important, but since the majority of diesel is fungible, one never really knows if the fuel has already been treated with Cetane at the refinery. The best approach, therefore, is to hope for the Cetane boost and focus on the other important components required such as Detergents, Stabilizers, Lubricity year round and during the winter, Deicers and both Terpolymers, Heavy Wax Modifiers and WASA (Wax Anti-Settling Additives).
Today’s ULSD fuel needs to be treated with an effective multifunctional additive package containing DW-10 Detergents, Cetane, Fuel Stabilizers and Lubricity Improvers and, during the winter, Cold Flow Improvers, Heavy Wax Modifiers and WASA, and Deicers. ULSD fuels that are properly treated provide excellent combustion which allows the conversion of available BTU’s into power.
ULSD fuels that are not properly treated year all year using DW-10 Detergents produce significant soot loading of the Diesel Particulate Filter [DPF]. When the DPF sensors detect back pressure due to soot loading, forced regeneration is required.
During a forced regeneration, a vehicle must pull off the road and, over the next 40 minutes with the engine set at high idle, diesel fuel is injected ahead of the DPF to burn out the soot.
Delivery trucks/vans, waste haulers, and school buses are all prone to forced regeneration because such engines do not reach highway operating temperatures. Passive regeneration occurs while the vehicle is driving down the highway. In this case, a small amount of diesel is injected ahead of the DPF which provides supplemental heat to burn out the soot.
Using a premium multifunctional additive consistently throughout the year reduces forced regeneration up to 80% and saves both time and money.
In addition, eventually, all DPF equipped trucks and vans will need the DPF filter to be removed and sent out for cleaning at an estimated cost of up to $1500.00.
Notably, some fleets using premium diesel additive packages have noticed improved fuel economy as well.
The DW-10 Test was developed to evaluate the detergent effectiveness of both Clean-Up and Keep Clean in the multi-event injectors installed in High Pressure Common Rail [HPCR] engines.
Today’s injectors pulse six times per combustion cycle and operate under the extreme pressure of 30,000 PSI as well as high temperatures using ULSD. The untreated, or base-line testing, revealed the tendency to produce external carbon deposits and Internal Diesel Injector Deposits [IDID’s] that form sticky deposits on the internal fuel metering valve. The IDID’s cause the fuel metering valve to stick open/closed or to open and close slowly. The formation of both the external and internal deposits result in power loss, increased smoke and emissions, reduced fuel economy, and increased soot loading of the DPF.
The DW-10 test requires repeat cycles followed by a hot soak between cycles. The total test time is 60 hours followed by injector removal for flow testing.
The standard detergent packages available ineffectively remove these deposits so new detergent technology has emerged to compensate for this deficiency. These detergents are tested to determine the specific treat rate to Clean-Up and then dosage drops down to a Keep Clean treat level.
These detergent packages are very robust and need to be used all year. Continuous treatment:
- Improves fuel economy
- Improves engine performance
- Reduces maintenance costs
- Reduces forced regen and passive regeneration
- Reduces emissions
- Maximizes engine life
Performance Diesel, LLC offers laboratory assessment services at no cost to our customers.
In the fall, we recommend that our customers test their primary fuel sources. In many cases, the Terminal Fuel is fungible which means that the diesel fuel meets the ASTM D-975 specification but the fuel is commingled.
Each fuel will have its own specific winter performance but, on average, the test results will be representative.
We urge fuel sample testing every month during the traditionally cold months from November through February as well.
Winter fuel sample testing comprises the following:
- Cloud Point
- CFPP
- Pour Point
We also offer the following additional lab testing options:
- Karl Fisher (water)
- HFRR (lubricity)
- Stability
- Flash Point
Complimentary laboratory test kits will be provided.
The EPA Clean Air Act set in motion the reduction of Sulfur in Diesel fuel. The EPA’s objective in reducing the Sulfur content was to reduce HC, SOx, CO, NOx and PM. Prior to 1994, the Sulfur level of both on-road and off-road diesel was, on average, between 1000-2500 ppm. In 1994, the maximum Sulfur level was reduced to 500 ppm for both on-road and off-road fuel. Then in June, 2006, ULSD (max 15 ppm Sulfur) was introduced for on-road fuel. Several years later, off-road fuel was also reduced to 15 ppm Sulfur.
Refiners used hydrotreating to reduce the Sulfur level. In addition, hydrotreating also lowered the aromatic content. The combined Sulfur and aromatics reduction caused significant lubricity issues resulting in single-stage fuel injector leaking. The injector O-rings with the higher aromatic fuel swelled the O-rings which kept the seals tight. The low-aromatic fuel caused the O-rings to shrink which lead to thousands of truck engines with leaky injectors. All these leaky injectors had to be replaced with non-shrinking O-rings.
When fuel lubricity problems appeared, the recommended test-method of assessment was the Scuffing Load Ball-On-Cylinder Lubricity Evaluator [ASTM D6078]. Due to poor correlation between the bench test and the real-world vehicle test, a new lubricity test was developed, the HFRR [ASTM D6079].
In 2006, the Sulfur content was reduced to less than 15 ppm for on-road fuel. In 2010, the Sulfur level of off-road fuel was reduced to the same level. Today, both fuels are identical, except for the addition of 25 ppm of automate red dye which designates off-road fuel as tax exempt.
In 2006, the HFRR lubricity specification was 520 micron wear scar (HFRR). The Engine Manufacturers Association’s [EMA’s] position was for fuel to meet a wear scar of less than 460 microns to improve lubricity.
The recommendation was therefore to add diesel additive packages containing an effective synthetic lubricity improver. It is important to emphasize that all diesel fuel should meet the EMA lubricity specification to prevent premature pump and injector wear.
When ULSD was first introduced in 2006, fuel lubricity was not the only problem that surfaced when the Sulfur level was reduced to less than 15 ppm. Fleets complained that the ULSD did not have the power and fuel economy was reduced by 1%.
The previous high sulfur fuel provided the following benefits:
- Natural increased fuel stability
- 50% longer fuel filter life due to low asphaltene formation
- Low moisture fuel because the Sulfur held the moisture until it was combusted
- Decreased microbial growth since Sulfur is a natural biocide
ULSD fuel is hydroscopic (it absorbs moisture). Biodiesel can hold up to 10 times the amount of moisture as compared to ULSD. Thus the combination of reduced Fuel Stability and increased Tank Water Bottoms today requires the implementation of a Tank Maintenance Program to control and help prevent the growth of Bacteria and Fungi. If left unchecked, the Bacteria and Fungus will produce slime and organic acids resulting in tank corrosion and plugged fuel filters. This problem will not go away so it is mandatory to implement a routine Tank Maintenance Program.
A very popular method to test in the field or in the lab is the Liqui-Cult Microbial Test Kit made by MCE Chemicals & Equipment. This testing procedure requires the Incubation of the Liqua-Cult for 30 hours for Bacterial Growth and 72 hours for Fungal Growth. We suggest using a marker to identify tank and test start time, day and date on the Liqui-Cult bottle. Once the time specifications are met, a careful comparison is required by comparing the sample bottle to the colored chart to determine the degree of contamination. The cost per kit is about $10.00.
The best approach is to be proactive and implement a Tank Maintenance Program for all bulk storage tanks, including customers’ storage tanks. It is estimated that over 50% of all tanks, when tested using a tank bottom sampling device, test positive for the growth of Bacteria and Fungus.
We recommend implementing a Tank Maintenance Program that involves testing all the tanks using a tank bottom sampling device. Due to the number of tanks that need to be tested, the best approach is to assume microbial growth, pump or drain tank bottoms until clear, and do a Shock Treatment on all fuel tanks using a Biocide and a moisture dispersant/tank cleaner. Once all the tanks have been cleaned, twice-a-year treatment using a Biocide and a moisture dispersant/tank cleaner is recommended. It is also important to treat the tanks every 3 months to keep the tank bottoms dry with Performance Fuel Polisher treating the diesel at 1/1000 to dehydrate the tanks. Remember, no water, no bacteria.
Tank Clean-Up Procedure
- Pump out or drain tank bottoms until fuel is clear.
- Properly dispose of sludge and water
- Add FQS 1.5 biocide at a rate of 1 gallon per 10,000 along with Performance Fuel Polisher at 1/500
- Fill the tank with fuel to the tanks’ operating capacity
- Wait at least 8 hours
- Sweep the tank bottoms to remove any settled debris
- Replace dispenser filter after 24 hours as it will catch any remaining contaminates
During winter, today’s ULSD diesel is causing many more winter operational problems as a result of Heavy Wax Drop Out. The problem of Wax Drop Out has been associated with the increased processing of Western Canadian Select-Tar Sands Crude [WCS]. WCS is being pipelined from Alberta, Canada to Superior, Wisconsin and south of Chicago.
For example, the BP Whiting Refinery invested six billion dollars to process this heavy crude and the Exxon-Mobil and Citgo Refineries near Chicago are also adding WCS to their crude slate. WCS today is selling at a discount of $15 – $20 per barrel but it wasn’t that long ago when the discount was closer to $40 – $50 per barrel less than West Texas Intermediate [WTI].
The normal rule of thumb is the maximum reliable winter fuel operability was 20°F below the fuel’s cloud point, but today, with diesel fuel containing Tar Sands, the reliable operability is closer to 10°F below the fuel’s cloud point.
The solution to this major problem is to blend considerable amounts of No. 1 or to use a winter additive package that contains Terpolymers, Heavy Wax Modifiers [HWM] and WASA [Wax Anti-Settling Agent]. It is important to note that conventional EVA-Copolymers may claim wax anti-settling but this level of protection is minimal, as the majority of the heavy wax will drop out of the diesel overnight or over the weekend.
The most effective approach is to use a winter additive package that makes the claim of containing WASA. With WASA technology formulated as an integral part of the winter additive, you regain the 20 degree delta below the fuel’s cloud point. In contrast, without WASA, the fuel’s winter operability will not be 20°F, but closer to 10°F.
Our petroleum laboratory has the ability to set up a static test of glass jars of fuel treated with your winter additive and glass jars treated with our antigel additive formulated with WASA technology. The glass jars are stored at 15 degrees below the fuel’s cloud point and, within 72 hours, the jar treated with WASA will be cloudy with minimal wax drop out and the other glass jar with typical winter cold flow chemistry will reveal significant wax drop out. This heavy wax that has settled is picked up at start up and severely plugs the fuel filters preventing the equipment from starting. This also is called diesel fuel gelling.
The bottom line is to not rely on CFPP laboratory results unless using a winter additive that makes the specific claim, “Contains WASA.”
An effective winter additive package must contain the following:
- Effective Terpolymer (three different polymers) which is much more advanced than an EVA-Copolymer (two different polymers)
- Effective Heavy Wax Modifiers [HWM]
- Effective Wax Anti-Settling Agents [WASA]
- Non-Alcohol Jet Fuel Type Glycol Ether Deicer in sufficient levels to depress the freeze point of 100 ppm of water down to 20°F